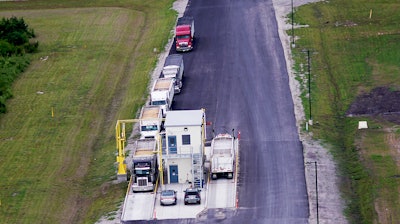
What technology can help a grain or feed facility with accounting, biosecurity,worker shortages, traceability, efficiency and customer satisfaction? Acontactless grain weighing and ticketing system.
Truck drivers are the lifeblood of the feed and grain industries. From delivering freshly harvested grain to delivering finished feed to the mouths of livestock, without them, very little product would move, and the modern agricultural supply chain would fall apart.
Drivers are essential, but they are also one of the most significant variables a feed manufacturer or grain handling manager will have to account for in their operation. It may be impossible to control what happens once a driver is on the road, but a contactless weighing and ticketing system can help managers control what happens with drivers on-site.
"Truck drivers don't need to get out of their vehicles and walk around on the scale platform for any part of the weighing process," explains Jonathan Sabo, VP of Marketing and Customer Support forCardinal/Detecto Scale. "Which avoids the potential for safety liability due to injuries."
Contactless grain truck identification
The "contactless" part of the system means much more than avoiding physical contact. Weighing and ticketing systems can be created to allow a driver to make their way through a grain facility without having to speak to an employee, and for the most advanced systems, one day, an employee will not even need to be on site.
This means that drivers will now only be limited by the speed of the equipment being used as they move through the system. There are many different levels of complexity, depending on what is right for your facility.
"Weighments can be as simple as ID entry using the proximity ID, with relevant data pre-entered into memory and associated to the ID, or full-blown WinVRS vehicle recording system data integration with all of its more sophisticated associated data recording," says Sabo. "Both of these systems allow for true contactless ticketing."
Automation reduces human errors, delays
Contactless weighing and ticketing systems start the same way as any other weighing and ticketing process by linking the truck to the contract for which they are hauling grain. With a traditional system, the driver needed to contact a facility employee by a speaker or going inside the facility or weigh house.
After contact is made, the employee is responsible for taking the driver's information, linking them to the right contract, and processing a sample taken by a grain probe. There is a risk of human error at each of these steps that can lead to delays or other costs.
"One of the strange things about the grain industry is somehow grain elevators got in the business of doing part the accounting for the farmers," explains Tim Ciucci, senior VP of Sales & Marketing atCompuWeigh Corp."Every time a farmer sends in a load of grain, you would think that 100% of that load is paid to the farmer.”
“But in truth, many farmers share ownership of the farm with others, and grain elevators have taken up the responsibility of writing as many checks to each owner rather than having the farmer figure it out. This is what's called a split account,” he said.
“The farmer may also have a different split depending on what field the grain is taken from. It can get complicated quickly, and part of what a contactless system does is place the decision of what contract is chosen onto the driver, not the scale house employee."
RFID tags enhance contactless weighing
At the lowest level, having a scale kiosk that allows a driver to select what contract they are delivering grain for, freeing up the scale house attendee to focus on processing the grain sample. But, with a few more pieces of equipment, elevators can upgrade to an almost completely automated process.
"For most grain elevators, fully contactless scale ticketing systems typically include the truck scale itself (either one scale or two for inbound/outbound weighing), plus a weight indicator, RFID reader – either short-range (typically scans 3-5 inches) or long-range (typically scans up to 15 ft and is more costly), RFID badges, remote weight display, related cables for connectivity, and vehicle recording system software on a PC," says Sabo. "These systems can all be easily installed by a scale service company."
Implementing RFID tags allows the grain elevator to do much more with a contactless weighing system.
"The goal for grain receiving is to keep the probe as efficiently as possible without having to help the drivers very much," says Ciucci. "And we accomplish that because each truck has given them an RFID tag."
How automated grain handling systems work
A truck moving through a grain elevator that is utilizing contactless ticketing and weighing will follow the following process:
- A scanner records the truck arriving at the grain elevator.
'By tracking how long a truck is in grain receiving, a grain elevator can show farmers how quickly they unload grain," says Ciucci. "Tracking how long a truck is at each point of the grain receiving process also lets the company figure out their slow points."
- The driver pulls forward to the scale house to be probed, and the RFID sensor marks its arrival. The truck driver is shown the most recent contract this truck drove for, but the driver can also select from their past contracts.
"Because the driver is picking it on the touchscreen," says Ciucci. "This also allows the probe attendants to become much more efficient. 90% of the time, the drivers are checking themselves in, they don't need to talk to the driver, all they're doing is grading faster than they ever did before."
- Once weighed and sampled, the driver is shown what dump pit to pull into on a digital display.
"Sometimes, when things are busy, a probe attendant selects the wrong pit for the truck because they're not paying attention to the moisture," explains Ciucci. "With automation, the software automatically selects the right pit."
- An alert is sounded if the driver has pulled into the wrong dump pit.
"You're keeping people out of the dump pit area by scanning trucks and confirming that they will go to the right dump pit," says Ciucci. "By preventing mixing corn and beans. Your company is eliminating the biggest mistake that elevators make, identifying the wrong truck."
- Once unloaded, the truck is scanned at the outbound scale, then weighed and given a ticket.
"When you go visit elevators, they can have 10 to 20 White trucks on-site at any one time," says Ciucci. "If somebody pulls over to use the restroom, the queue gets out of order. Then when they weigh out, it's easy to make a mistake and mix up two trucks. At that point, the elevator has screwed up two tickets. RFID tracking eliminates this mistake."
- A final sensor records when the truck leaves the grain elevator.
Keeping grain truck drivers safely in their seats
When visiting a grain or feed facility, the best place for a truck driver to stay is in the truck's cabin. Every time they leave, they create a delay in the loading and unloading process and, more importantly, a safety and biosecurity risk.
In 2015, theUSDA's Animal and Plant Health Inspection Service(APHIS) released a study [this is too vague, link the name of the study instead] to identifyhighly pathogenic avian influenza (HPAI) transmission pathways. The disease had recently been responsible for the loss of millions of birds, and stakeholders across the industry wanted answers on what was responsible.
虽然结果不确凿,相信that one of the factors was a failure of biosecurity at the poultry farms. One of the biosecurity failures was allowing the movement of vehicles and people between different sites, like the drivers and trucks that deliver feed.
The transmission of avian influenza and other livestock diseases like porcine epidemic diarrhea virus and African swine fever have changed the way the industry looks at biosecurity, and one of the easiest steps in biosecurity is keeping drivers in trucks.
The safety implications are also easy to see. When drivers leave their trucks, facility staff and management now have an unknown variable in their safety plan.
Remember, a driver may not have been trained on safety at your facility or the industry, may not have proper PPE, and has more than likely put themselves into the dangerous situation of being around moving traffic and possibly moving grain.
By not doing all they can to keep drivers inside their trucks, facilities are creating an unnecessary risk to facility staff and the driver themselves.