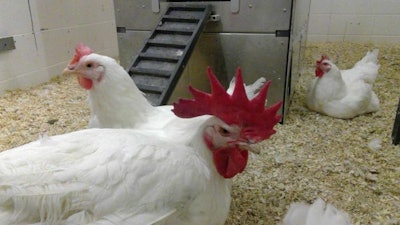
How the technologies of the future are taking the guesswork out of animal feed production
At a research facility in Canada, the chickens raised byProfessor Martin Zuidhoffeed themselves.
Zuidhof, a professor of poultry systems, modeling and precision feeding at theUniversity of Alberta, has developed an automated broiler breeder feeding system that provides rations according to the needs of individual birds — hopefully bringing an end to to the longstanding challenge of flock uniformity. In the system, each bird is outfitted with an RFID tag to identify it to a computer system with data about the bird’s ideal body weight. When it walks into the feeding area, it stands on a scale that allows the computer to determine how much the bird should be fed — more if it’s underweight, less if not — and the appropriate amount of feed is dispensed.
The system may be a step toward the feeding system of the future, but Zuidhof and other experts in the field don’t believe it’s the final stop. In perhaps 10 to 20 years — assuming we aren’t all eating cultured meat —precision feeding systemssimilar to Zuidhof’s may be capable of dispensing truly individualized rations that cater to specific nutritional needs by mixing ingredients on-site.
When chickens walk into the feeder, it weighs the bird and distributes a specific amount of feed based on the animal’s target weight. (Martin Zuidhof)
NIR utilization
Some of the technologies needed to make the sort of on-site, real-time feed mixing Zuidhof envisions have yet to be invented. There’s a significant need for sensor technologies capable of measuring key indicators of animal health, for example. There’s also a need for more research to determine which indicators matter most.
But at the other end of the supply chain, poultry nutritionist Logan Erb is already implementing one critical technology that already exists: near-infrared spectroscopy, or NIR.
NIR measures the way near-infrared light bounces off a substance, and uses data about how the light is scattered to take measurements of the sample’s properties, according toJohn Boney, the Vernon E. Norris Faculty Fellow of Poultry Nutrition atThe Pennsylvania State University. It’s not a new technology, but its use at feed mills around the world is growing as science continues to advance the kinds of properties it’s capable of detecting.
NIR, Erb said, helps him achieve nearly every major goal he strives to meet as a feed nutritionist. AtKalmbach Feeds, where Erb has worked since graduating from Penn State last summer, certain ingredients such as soybeans and corn are analyzed using NIR to determine their protein content as each load arrives. If the quality of a shipment doesn’t measure up to what they were promised, Erb said, they may contact the supplier to ask for a refund — protecting the quality of the feed, and its monetary value.
Once the nutritional value of the raw ingredients is verified, Erb uses that data to adjust his feed formulations. If the corn received during the past month or two has run low on amino acids, the mill may add some additional aminos to the mix. But if the corn is actually higher in amino acids than generally expected, the mill can save money but cutting back on the amount of synthetic amino acids without hindering the feed’s performance.
NIR is also used to check the finished feed to ensure specifications provided to customers are accurate. Kalmbach retains a sample of each load of feed for up to a year in case a customer reports difficulties.
Although NIR has added some new tasks to his workload, Erb said, on the whole, it’s making his job as a nutritionist easier.
“You’re much more confident in the feed formulation,” he said. “At the end of the day, it’s good work — it will make our product better and more competitive.”
It’s also, Erb said, only the beginning. Kalmbach is in the process of expanding and upgrading its in-house laboratory to further increase its capacity for in-house nutritional analysis and research. If a customer’s birds go off their feed today, he said, it may take two weeks to get necessary data from an outside lab. “Hopefully in 2-4 years, we’ll be able to analyze it right away and figure out what happened,” Erb said.
In the future, specialized feeding systems could be capable of blending specific diets catered to an animal’s unique nutritional needs. (Martin Zuidhof)
Precision formulations
The ability to formulate feed according to the price amount of protein in a load of corn or soybeans may have implications enough for feed mills, but according to researchers, the use of NIR in feed mills is still relatively limited when compared to the technology’s raw potential.
NIR, Boney explains, is only as good as the reference data used to determine exactly what you’re looking at when you run a sample through the scan. Currently, feed mills have access to data that enables analysis of major nutrients such as protein, fiber, moisture and ash. Next on the horizon, Boney said, is reference data for other concerns — toxins and anti-nutrients for example. Work is also underway to enable NIR to look for mineral content; enzymes, probiotics, and specific feed additives are all possibilities.
“Anything you can put into the feed has the ability to be measured if the money is invested in creating the references,” Boney said.
Although futuristic, it’s not unrealistic to think that NIR could one day be used on a feed ingredient like bakery byproducts, or even food waste, to determine the nutritional value of such a product and design a feed formula to fill in the gaps, Boney said.
“This is how NIR can work, and will work,” he said. “You’ll have a nutritionist on staff who comes up with the nutrition plans and programs and then, under that person, you’re going to have formulators. And the formulators are going to trace down what ingredients we have here, what are the current specs based on the NIR results, and then use the NIR results to update the matrix and formulate to that specific batch of whatever that ingredient is.”
Automated feeding could complete the chain, Boney continued. Sensors could scan livestock to determine health and body condition, and rather than feeding a precise amount of a single feed, the automated system could create an optimal diet for a specific animal by blending multiple bins of NIR-verified feed mixes.
It’s not commercially available yet, Boney said, but the technologies needed to make it a reality are already in development.
Decreasing feed costs, improving efficiency
Although the prototype of Zuidhof’s feeding system in Canada works well, the cost exceeds the benefits associated with improved flock uniformity and decreased waste. Even so, Zuidhof believes it will be possible to make the feeder commercially accessible in the near future — he is working with an engineering firm to bring the cost within practical margins.
But given the time and investment needed to create an all-around mixing and feeding system, why bother inventing one at all? Zuidhof believes that once the technology is available, it will benefit all aspects of animal production.
Improved feed efficiency will reduce costs, Zuidhof said, but along with that comes all the accompanying environmental benefits.
“If you feed what the bird needs, it will minimize the excretion of unneeded nutrients,” he said.
Feeding on demand could also come with important health and welfare benefits, Zuidhof said. Ongoing research already shows the precision feeding system causes chickens to act more calm throughout the day. And there’s reason to believe it could reduce illness. A lack of food for as little as 6 to 12 hours is known to predispose chickens to enteritis and other conditions, so more frequent feeding, Zuidhof said, should improve gut health.
“I’m focused less on the right feed and more on the right quantity right now,” he said, “but there’s a tremendous amount of potential in terms of feeding the right feed to the right bird at the right time.”
Announcing the Feed Mill of the Future digital supplement
WATT’s feed brands Feed Strategy and Feed & Grain magazines join forces to launch the monthly Feed Mill of the Future digital supplement. Each edition aims to provide animal feed industry stakeholders with forward-looking content, market insights and a spotlight on the leading-edge technologies shaping the global feed industry of tomorrow.
Subscribe today!https://bit.ly/3dWzow7